Having outlined a new vendor-agnostic, lab-based “pre concentration screening test” for mining in part one of this three-part series, SRK is back for part two, discussing the wider pre-concentration evaluation process that this testing fits into
“With any pre-concentration analysis, we need to, first, understand the heterogeneity of the deposit; simply put, if you don’t have heterogeneity, you don’t have the ability to separate the good stuff from the bad stuff and carry out pre-concentration,” Bob McCarthy, Principal Consultant, SRK Consulting (Canada) Inc, says.
With this baseline in mind, SRK Consulting has devised a pathway for companies with drill core at their disposal to analyse whether pre-concentration is a viable option for their flowsheet.
Made up of five steps, this staged approach is deliberately designed to allow companies to pause at the end of each phase to re-evaluate if there is a strong enough case to continue investing the time and finances required.
The heterogeneity analysis is first up, which, under SRK’s evaluation, includes two different approaches based off drill hole analysis: Heterogeneity and Scale and Composite-Sample Relationship Analysis.
“Heterogeneity and Scale involves a process of looking up and down the bore hole at different aggregation distances from every sample and interrogating the sample grade – or net smelter return – against the aggregations above and below that individual sample,” he explains. “We then increase the size of the aggregation to see how that relationship changes.”
Such analysis enables SRK experts to derive the heterogeneity measures typically dubbed ‘waste in ore’ (mineralisation below the cutoff grade within an above cutoff grade zone) or ‘ore in waste’ (mineralisation above the cutoff grade within a waste or marginally below cutoff grade zone). Using a cutoff grade derived from industry benchmarking, the consultants assess the aggregation distance, as resolved in the vertical direction, with the “selective mining unit” (SMU), which typically relates to equipment sizing for mining.
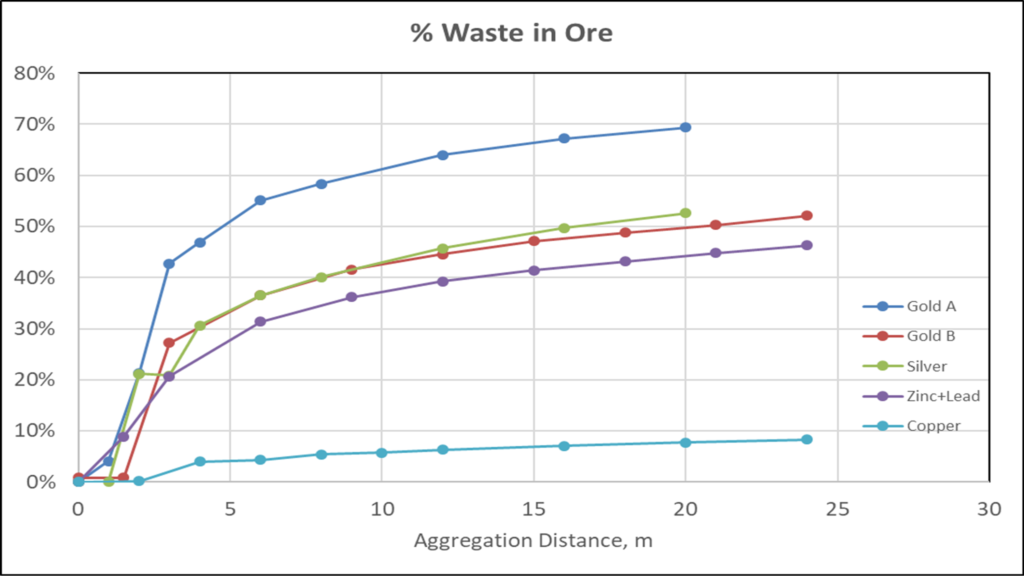
“The pitfall some companies go down is picking your SMU to match an equipment size and production rate typically aligned to a corporate or strategic objective,” McCarthy says. “This could mean generating a 12-14-year mine life for a gold operation, or some other investor-led metric that doesn’t necessarily respect the deposit’s heterogeneity.”
The second approach – Composite-Sample Relationship Analysis – allows consultants to further quantitatively assess those waste in ore/ore in waste heterogeneity measures.
“Those parameters have multiple uses after being determined,” McCarthy says. “For example, they help guide in the sample selection – you can even visualise them in 3D with something like Leapfrog. You can also see contiguous lengths of above or below cutoff grade material in ore zones or marginal waste zones, representing what an ore sorter may see. These would be targeted for testing.”
Responding to industry calls, SRK now offers a step between this fundamental heterogeneity analysis and the test work it can conduct at Base Metallurgical Labs’ Kamloops facility in British Columbia, with what McCarthy calls “size the prize” economics. It provides insight into possible pre-concentration strategy outcomes and, just as important, justification to continue to the next step of lab test work.
This process – carried out by SRK on several projects in the past – is designed to allow the mining company and consultant to test pre-concentration strategies from an economic perspective, assessing if an operation should be removing waste from ore or looking to recover above cut-off grade material from “marginal waste”.
McCarthy added: “It is about answering these questions: is it best to remove waste from mill feed, and to what maximum grade of feed, or to extract mineralised material from marginal, below cut-off grade material that increases the mineral reserve? And, of course, do the expected results of this process look promising?”
Gold is a good example here as the economic case study for pre-concentration often only stacks up when a “cap” is applied to the grade of ore subjected to pre-concentration. In other words, the highest-grade material should not be targeted. Even high-efficiency pre-concentration methods incur some metal loss, and any amount of “loss” that occurs in a gold project is difficult to make-up within a conventional flowsheet.
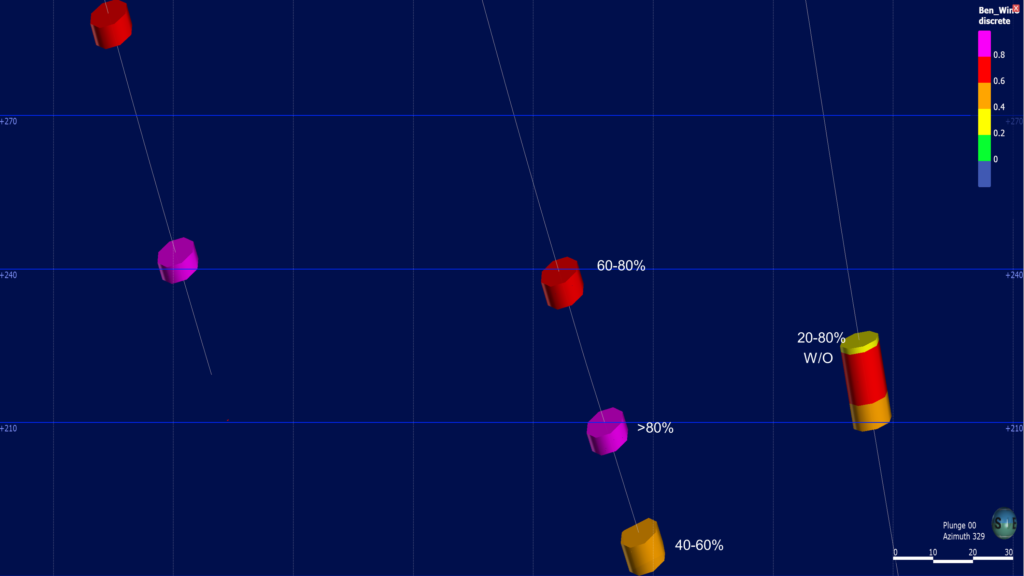
The third step in this five-step process is the lab test work McCarthy’s colleague, Adrian Dance (Principal Metallurgist at SRK Consulting), previously outlined in detail in the first article in this three-part series.
The “pre-concentration screening test” leveraging X-ray Transmission based sensor technology can not only indicate pre-concentration amenability, but also provide key inputs into the pre-concentration strategy selection and evaluation, Dance says. He says the testing offers an assessment of pre-concentration potential, as well as an estimate of material bypass and metal upgrade from samples as small as half cores.
Used in conjunction with crushing and screening, this testing rapidly – and cost effectively – assesses the potential for pre-concentration, which can then be applied to scoping or pre-feasibility studies, according to SRK and Base Metallurgical Labs.
Which is where steps four and five of the SRK evaluation – mine planning and mine economics – come in.
“With the heterogeneity measures assigning the distribution of waste in ore, ore in ore, and ore in marginal material in mining block models, the test results reflecting these conditions can be populated into those same models for mine planning,” McCarthy explains.
Typical mine planning steps of pit/stope optimisation, mine design and scheduling can proceed on the assumption of one or more pre concentration strategies, with different versions of mine schedules, reflecting different pre concentration strategies, evaluated.
This type of analysis typically works for a project in pre-feasibility study stage, where engineers can go into the existing block model, bringing the results from the heterogeneity and lab tests into the mine optimisation, design and scheduling process that takes place.
“The challenge is that the scheduling needs to assume a certain strategy – maybe you have determined what that strategy is close enough with the ‘size the prize’, but there are always a few elements you may want to tweak,” McCarthy says. “This could be the mass pull, or waste rejection targets, for instance.”
As a result, sensitivity analyses – mostly numerical tweaks – are embedded in the process.
When not dealing with a pre-feasibility-level project, the SRK team typically rely on an existing schedule that has been run during a scoping study or preliminary economic assessment. This model is modified and tested with different schedule scenarios and pre-concentration strategies based on the heterogeneity measures (step 1) integrated with the lab test results (step 3).
Out of the mine planning step comes a schedule that would go onto the next step: mine economics modelling.
“The model is configured to take in the heterogeneity measures, recovery curves, etc to change the amount of metal reporting to revenue and so forth,” McCarthy says. “Once I get schedules – based on the upgraded block models or it may be a pre-existing schedule – I would then put them into an economic model that has all the levers to pull for different pre-concentration strategies.”
Such a stepwise approach is indicative of where the mining industry is at the moment with vendor-agnostic pre-concentration analysis, enabling companies to get comfortable with the data and assessments as their understanding of their deposit’s heterogeneity grows.
There are potential refinements and fine-tuning opportunities too.
For example, if SRK was gifted with drill core or assay data that was more granular than the 1-2 m intervals typically taken at the exploration stage, it could indicate with greater certainty how particle sorting – typically analysing grades at intervals around a few centimetres – could benefit the deposit in question.
Also, if mine modelling software had matured to the point where block models could be tailored specifically to these waste-in-ore and ore-in-waste characteristics, SRK could segregate the areas in question, instead of applying the type of dilution factors they currently have in place to account for the grade-based realities. This would more clearly communicate the deposit’s heterogeneity to all stakeholders.
Yet, McCarthy and Dance know this will come in time, and are happy to work within the current confines to continue the industry’s education process and identify where the pre-concentration opportunities are
Further discussion on this and what SRK’s pre concentration analysis evaluation – with that embedded pre-concentration screening test – means within the broader mining industry context will follow in the final article in this three-part series later this year